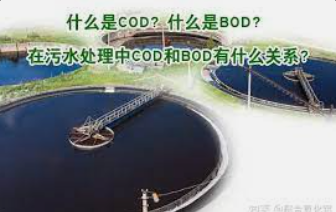
近年来,随着成品油质量标准不断提高,油品中添加剂的种类不断增多,处理船舶含油污水所用的进水水质日趋复杂,传统的含油污水处理工艺(重力分离和过滤工艺)已不能满足复杂水质的处理需求,各项出水指标已不能达到相关废水排放标准的要求,需采用其他工艺对该工艺进行优化,以确保含油污水治理达到标准的要求。
1、船舶含油污水来源
船舶油污水主要包括船舶正常操作过程中排放的含油压载水、含油洗舱水和机舱含油舱底水等3类。
1)含油压载水是指油船在港口卸货之后向其货油舱内注入的压载水与舱内的残油混合形成的油水混合物。传统含油压载水中油的浓度很高,可达3000~5000mg/L,油珠主要以上浮油和分散油的形态存在。含油压载水中油的分布极不均匀,其中:上层为浮油层,含少量水,厚度一般在15~50mm,少数达100~120mm,中间层主要是水,含少量油,油的浓度一般在20~500mg/L,2号站登录下层为油泥层,含少量水和固体杂质。
2)含油洗舱水是指在清洗油舱过程中产生的含有油污的清洗污水。在检修油舱过程中,有些金属需要润滑、冲洗,由此会形成一1定量的含油污水。此外,装油货舱在更换装载油品的种类时需进行彻1底清洗,将原有的油品洗净,这也会产生含油污水。含油洗舱水的主要成分是油、泥沙和铁锈,此外还有各种洗涤剂、化学添加剂和微量的酚等。传统含油洗舱水中油的含量较高,2号站线路测试油的浓度平均可达30000mg/L,有时高达200000mg/L,且主要以乳化油的形式存在。当前,随着科技不断进步,在清洗船舶过程中会投入各种化学添加剂来降低污水中油的含量,因此含油洗舱水中油的含量已大大减少。
3)机舱含油舱底水是指船舶机舱内各种设备运行过程中和对这些设备进行清洗过程中产生的润滑油、燃料油和水的混合物。机舱舱底水中含有船舶使用的各种油类和化学添加剂,含油浓度大多在2000~5000mg/L,其中70%为润滑油。添加剂中的各种表面活性物质与燃料油和润滑油混合,促使机舱含油舱底水中相当多的油分以乳化油的形态存在。机舱含油舱底水的年平均发生量一般为该船总吨位的10%左右。
2、传统船舶含油污水处理方法
传统船舶含油污水处理的主要方向是去除水中的乳化油,降低出水的含油量。传统含油污水的成分极其复杂,油品的种类较多,其中有很多活性剂等化学试剂,致使其乳化程度较高。因此,传统含油污水处理工艺[2]主要以物理工艺为主,并辅以破乳工艺,根据油与水的密度不同对油和水进行分离。
2.1 破乳+气浮工艺
破乳+气浮工艺是船舶含油污水处理主要的工艺,处理流程简单(见图1)。含油污水首先流入混凝反应装置内,通过加药泵加入混凝药剂,使其与含油污水混合和絮凝(常用的混凝剂包括碱式氯化铝PAC和聚丙烯酰胺PAM等),经过一1定时间的混凝反应之后完成破乳+混凝,在含油污水中形成可吸附细小油珠的絮体,随后经过气浮装置,利用气浮设备产生的微小气泡完成油、絮体和污水的分离。该工艺具有操作简单、维修方便和运行成本低等特点。